
本研究基于断裂面条纹间距分析了AZ91镁合金的断裂行为,以预测疲劳高周疲劳寿命。起初,根据巴黎法律提取方程和关系。然后,使用ImageJ软件和热处理的Mg-Al-Zn合金断裂表面的场发射扫描电子显微镜图像测量条纹间距,这些合金含有和不含1%稀土元素(1%RE)。
最后,计算和校准了巴黎法的常数。结果表明,添加1%的稀土可以减小条纹间距,增强抗疲劳性(14%至40%)。此外,寿命散射带和平均误差分别从±2.7倍下降到±1.5倍和从150倍下降到33%,作为推荐模型的精度。
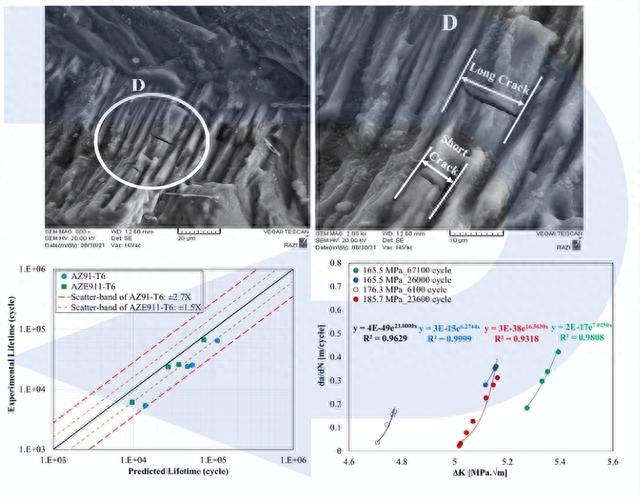
热处理将Mg基体上的连续析出转化为叶片状析出,显著减小了晶粒尺寸。添加1%的RE形成了新的铝,并在铸件缺陷之间创造了更好的分布。此外,AZ91合金中的疲劳条纹比AZE911 + 1% RE(AZE911)合金具有更大的曲率和不连续性,并且更显着和更粗糙。
镁合金是未来和绿色工程合金,广泛应用于汽车和航空航天工业。上述行业中的许多镁合金应用都与优异的机械性能有关,例如重量轻,最高强度/硬度比,良好的铸造和加工,可热处理能力和良好的生物相容性。
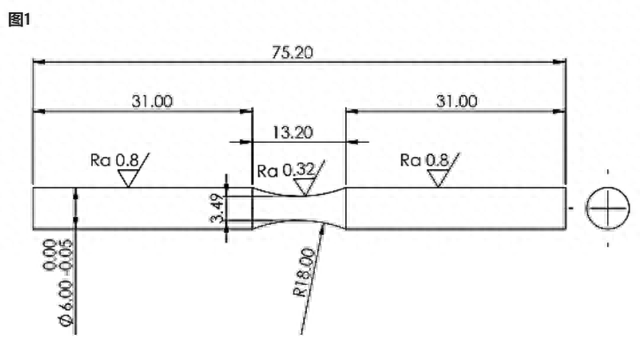
AZ91D(9%Al–1%Zn)合金是制造气缸盖最常用的镁合金,由于耐受非常高的温度和负载率,气缸盖在不可预测的时间失效或断裂。在下面的文献综述中,提出了一些模型和方法,研究人员已经用这些模型和方法预测了不同材料在1%RE和纳米颗粒添加,热处理的影响下的寿命。
McCullough等人测量了热处理6061铝合金的微观结构和物理裂纹,以预测低周疲劳(LCF)寿命,使用多级疲劳(MSF)方法和Coffin-Manson方程来计算扩展上述裂纹所需的循环次数。
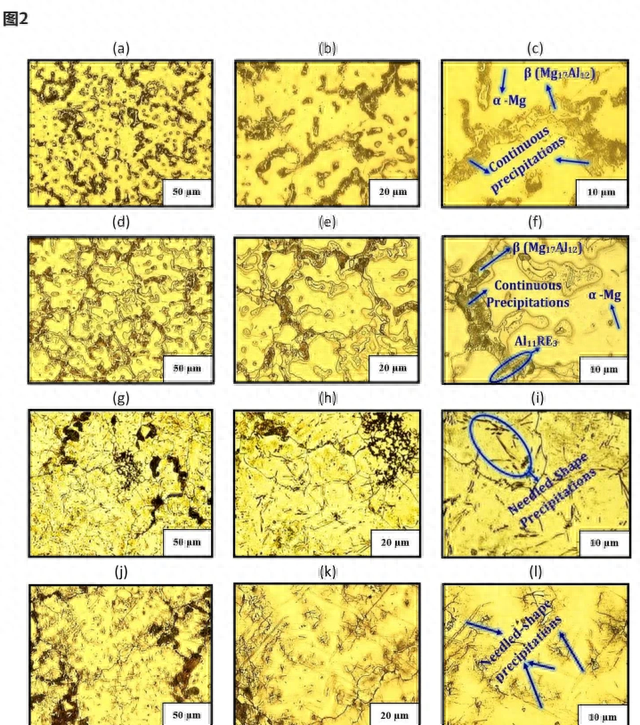
结果表明,实验寿命与MSF预测寿命之间有适当的一致性。Al-Buriahi等人使用窄光束几何中的蒙特卡罗模拟对一些化学材料的质量衰减参数进行了实验和分析。他们发现实验结果和蒙特卡罗模拟结果之间存在合作协议。
Yang等人使用SEM,光学显微镜(OM)和数字图像相关(CID)获得了钢4340和铝7075-T6合金裂纹尖端的塑性区域直径。DIC软件的SEM图像研究指示了应变场并计算了塑性区直径。然而,他们发现钢合金塑性区直径的理论和实验数据之间有很好的一致性,但铝合金则不然。
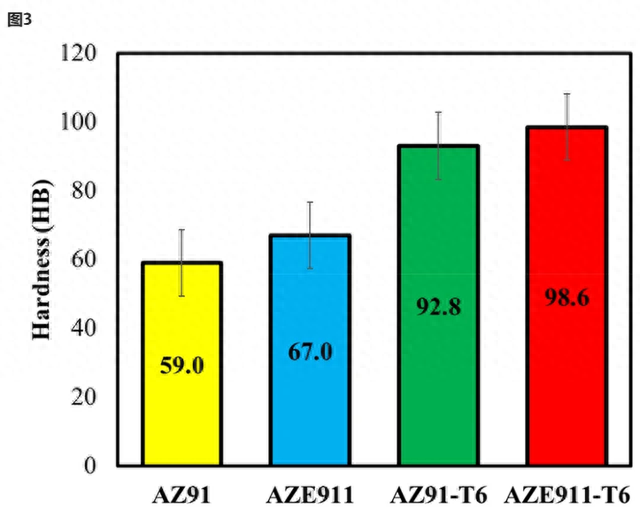
Kohler等研究了型腔尺寸和裂纹长度对AZ91和AM50合金疲劳极限预测的影响。利用巴黎定律,他们提出了疲劳极限预测的分布函数,在Kitagawa-Takashi图和EI Haddad&Topper方法中描绘了S-N数据和裂纹长度。
Ishihara等人提出了一个概念,即使用蒙特卡洛模拟来预测受铸造缺陷尺寸影响的AZ91合金的疲劳寿命,以评估疲劳寿命分布(由Weibull分布表示)。他们发现,通过增加铸件缺陷尺寸和应力水平,疲劳寿命的散射带增加,反之亦然。
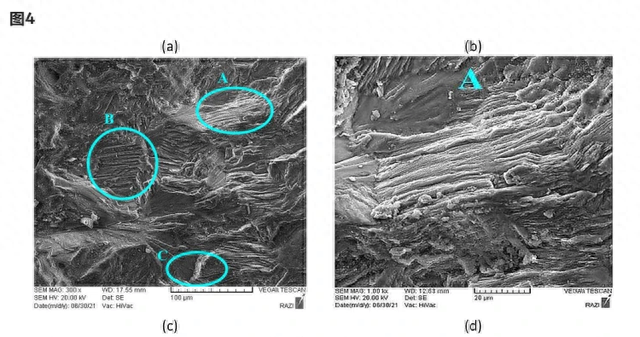
Bag等人研究了固溶和时效处理对AZ91 + 10%SiC合金疲劳行为的影响。他们的结果表明,与固溶处理相比,老化处理对降低裂纹扩展速率(条纹间距)和改善应力-应变行为的影响更显著。Uematsu等人使用有限元法(FEM)、修正的Green-Sneddon方程和5D权重函数方法的组合方法,评估了搅拌摩擦处理(FSP)和T3热处理对估计裂纹扩展速率的影响。
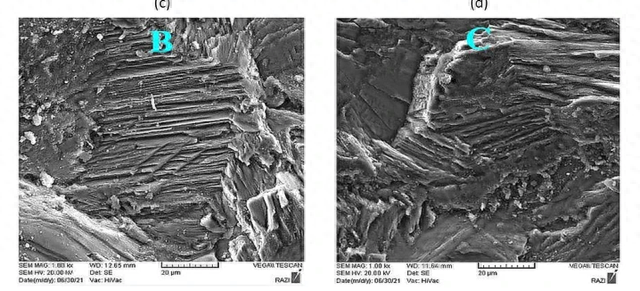
他们发现,FSP显着提高了疲劳极限(从50MPa到85 MPa),并降低了疲劳裂纹扩展速率。小林等报道,T4固溶处理显著降低了裂纹扩展速率,延长了疲劳寿命。而T6a和T6b老化处理具有相反的效果,因为它们不影响谷物和镁17铝12AZ91合金显微组织中的相析出。Venkateswaran等人使用巴黎定律描述了应力水平、裂纹尺寸和缺口深度对AZ91-T6合金裂纹扩展速率的影响。他们发现了巴黎常数的特定最佳值,并观察到裂纹扩展速率更多地取决于裂纹尺寸和缺口深度,而不是施加的应力水平。
Yang和Liu研究了添加1%铈对AZ91合金HCF性能的影响。他们的结果表明,添加1%铈后,疲劳极限为107周期增加了约30%,并且在相同的裂纹扩展速率范围内(10–3–10–6mm/周期),根据巴黎定律,应力强度因子范围(∆K)从2–4.5增加到3–6 MPa√m。

此外,裂纹路径转换为一些疲劳锯齿状和刻面条纹。在另一项研究中,Yang和Li 使用上下载荷方法描述了添加0.5%,1%和1.5%钕对AZ91合金耐久性极限的影响。他们指出,添加1%的钕对提高耐力极限(85 MPa)的影响最大。
Xu等人介绍了添加1%混金属态稀土元素(1%MM)对AZ91合金疲劳寿命和硬度的影响。他们得出的结论是,添加1%MM后,通过控制铸造缺陷的数量和大小,疲劳寿命增加。Zhang等人使用曼森-棺材定律、巴斯昆方程和MSF寿命模型来预测AZ91-T6和NZ30K04-T6合金的LCF和HCF寿命。
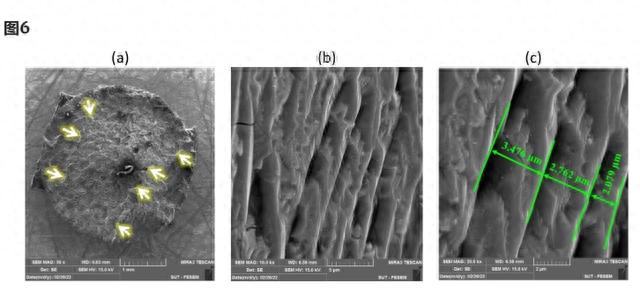
Mokhtari等人分析了添加1%RE对AZ91合金HCF性能的影响。他们说明了疲劳极限在106循环次数从65 MPa增加到105 MPa(增加62%),并且由于Al的形成,抗裂纹扩展速率增加3阶段。Olyia等声称,由于微观结构的变化,热处理将AZ91和AZE911镁合金的抗疲劳性和疲劳极限分别提高了14%至60%。
此外,AZE911-T6合金表面断裂中细条纹的聚集小于AZ91-T6合金。Maruschak等提出了一种基于断裂面数字分形图像分析的34KHN3M-T5钢合金寿命预测新方法,该方法包括三个阶段。第一阶段是根据局部最小值定律通过图像二元化检测条纹间距。第二阶段是使用霍夫变换旋转/旋转图像的高亮片段。第三阶段是计算连续线之间的空间。
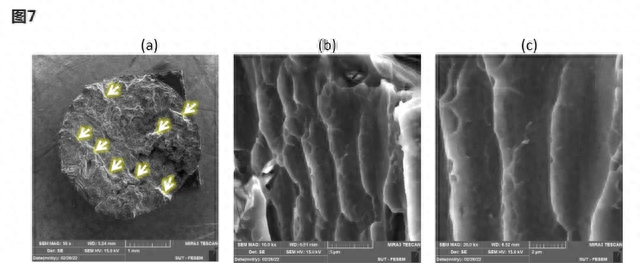
此外,他们还使用SEM图像测量了条纹间距。他们报告了两种方法的结果之间的小错误。Maruschak的研究与本研究的共同特征和区别是分别使用冶金软件和数字图像处理的SEM图像测量条纹间距。没有研究人员几乎直接通过测量条纹距离/空间来估计AZ91和AZE911镁合金的HCF寿命。1%稀土和不同热处理同时作用下的巴黎裂纹扩展规律是本研究的一项创新。
测试了一种铸造镁铝锌(AZ91)合金,以分析HCF寿命和抗疲劳性。首先,AZ91锭在电阻炉中在1°C的“二氧化碳气体+ 134%氢氟碳-720a”的受控气氛下熔化。然后,将67%的铈,23%的镧,7%的镨和2%的钕加入熔体中。将熔体在720°C下保持0.5h,在钢棒中搅拌60 s,然后在底部填充的钢模中以200 °C预热。 在这项研究中,新的镁合金被命名为AZE911。

溶液和老化处理在CO的受控气氛下进行,用于保护合金免受ATRA公司ATE1100L卧式管式炉中表面氧化和表面熔化的气体。首先,在5 h-415 °C下进行溶液处理。 然后,对AZ1和AZE3合金分别在5°C和7、215、160和185 °C下进行200、230、1和9 h的911次时效处理。3 h-215 °C和5 h-215 °C的时效处理对AZ91和AZE911合金硬度改善(增强HCF行为)的影响最大。因此,选择这两种老化处理并将其应用于机加工试样进行HCF测试。值得注意的是,“T6”的符号用于表示热处理条件,与特定标准无关。
硬度测试采用布氏方式和ASTM E10-14标准,由直径和载荷分别为0.1厘米和1500公斤的钢球压头进行。对每个样品重复硬度测试多达4次。使用的硬度计是通用的硬度测量机(KOOPA公司的UV1型号)。对于金相分析,将样品蚀刻在乙酸二醇溶液中,包括20ml乙醇酸(C2H4O2), 1毫升硝酸(HNO)3), 60毫升乙二醇(C2H6O2)和20ml蒸馏水。通过光学显微镜(OM)(Leitz公司的HM-LUX模型)分析了样品的微观结构。
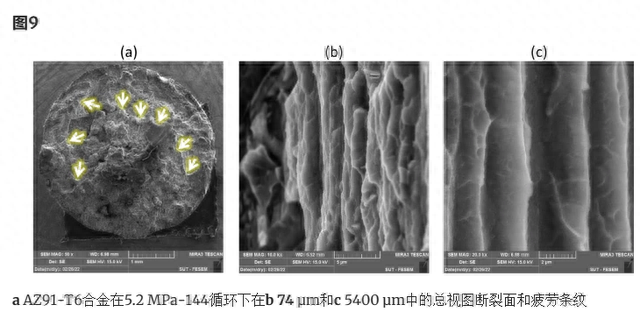
使用91点旋转弯曲疲劳测试装置(SANTAM 公司的STF-911型号)对热处理的AZ2和AZE600合金试样进行了HCF测试,根据ISO-1143标准,使用CNC机床将散装样品加工成圆柱形。在 AZ91-T6 样品的 HCF 测试中施加的应力水平分别为 115、125、135 和 145 MPa,AZE911-T6 样品的应力水平分别为 155、165、175 和 185 MPa。
对于所研究的两个人来说,这些压力水平并不相同。因此,通过选择上述应力值,考虑了类似的疲劳寿命范围。载荷是完全尊重的条件,平均应力、应力比(R)和载荷频率分别为零、−1和100 Hz。

Farrahi等人提出了一个模型,根据热处理影响下每个循环中的塑性应变能密度、施加的平均应力水平和测试环境温度,预测气缸盖Al-Si-Mg合金的LCF和热机械疲劳(TMF)寿命。他们声称,与其他模型相比,该模型具有较低的散射带和较低的气缸盖Al-Si-Mg合金的相对误差。
他们分别报告了±1.32X和±2.65X作为Al-Si-Mg合金LCF和TMF寿命的散射带范围。另一方面,TMF寿命的最大和最小相对误差值分别为17.7%和3%,LCF寿命的最大和最小相对误差值分别为62.3%和11.4%。

此外,LCF校准的标准误差为0.72%,其模型对LCF和TMF寿命的决定系数分别为0.8618和0.8455。Farrahi等人与当前研究之间的共同点提出了一个准确的寿命预测模型,具有最窄的散射带,最高的校准和最小的相对误差百分比。
McDowell等人开发了一个多倍模型来预测热处理Al-Si-Mg合金的寿命。在第一步中,他们发现了树突状蜂窝织的大小、晶粒、裂纹长度和铸造缺陷。在第二步中,他们基于塑性剪切应变、破坏机理中的有限元和曼森-科芬方程对裂纹孵化(夹杂物和孔隙中)和裂纹积累(夹杂物和孔隙中)和裂纹积累(缺口)进行了建模。在第三步中,他们模拟了裂纹尖端的放置。在第四步,他们计算了裂纹孵化的疲劳寿命,这取决于高循环和低周期状态下的累积系数和短裂纹。
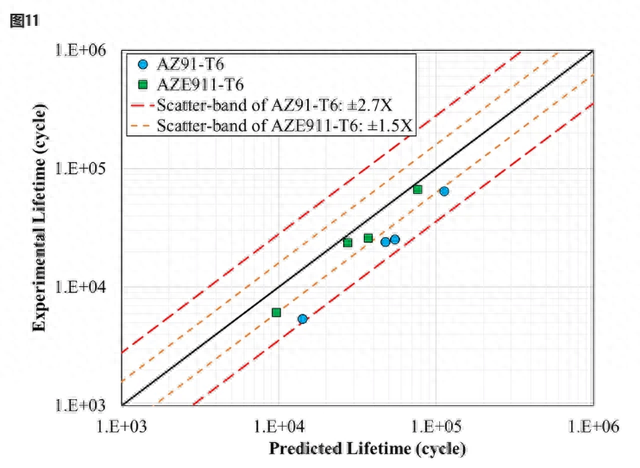
许多研究人员分析了疲劳条纹间距、铸件缺陷尺寸和裂纹尺寸作为重要的断裂痕迹对LCF/HCF寿命的影响,因此,作为脆性断裂最明显的标志,解理和准解理的大小和数量的影响可以作为新的研究进行讨论。
目前的研究研究了AZ91-T6和AZE911-T6镁合金的HCF寿命和抗疲劳性。结果如下:

添加1%稀土后,条纹间距减小,抗疲劳性增强(14%至40%)。添加1%RE将寿命散射带和平均误差分别从±2.7倍降低到±1.5倍和从150倍降低到33%,作为推荐模型的精度。热处理将连续析出转化为Mg基体上的叶片状析出,并减小了晶粒尺寸。

1%的稀土添加形成了新的Al11RE3相,并在铸造缺陷之间产生了更好的分布。AZ91合金的疲劳条纹比AZE911 + 1% RE(AZE911)合金具有更大的曲率和不连续性,并且更广泛和更粗糙。所提供的模型能够通过失效后断裂面上的条纹间距来预测汽车零件的HCF寿命,这对机械工程师修改和增强预测很有帮助/有用。
当前研究的主要挑战是实验数据数量有限。如果测量条纹间距的数据点较多,最终结论将更加可靠。此外,该方法可用于其他材料,以找到所有结构的独特模型。这项工作将用于进一步调查以找到一个全面的模型。