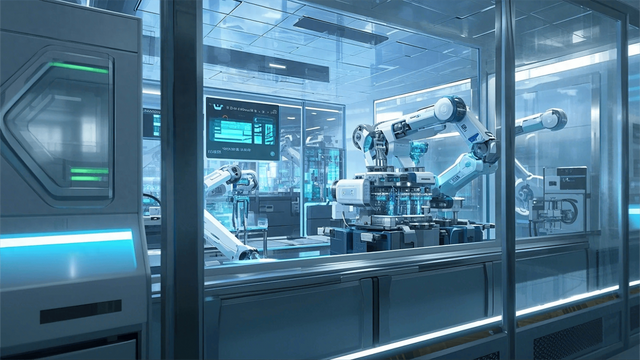
在工业4.0与数字化转型背景下,设备管理系统正经历从传统人工巡检向智能运维的深刻变革。本文将从技术架构、实施路径和典型应用三个维度,深入解析设备远程监控与预测性维护系统的实现方法。
一、智能运维体系的技术支撑架构感知层技术矩阵
(1)多模态传感器网络:集成振动、温度、压力、声学等工业级传感器,通过NB-IoT/LoRa实现低功耗广域连接。某石化企业部署的传感器阵列可实时采集3000+设备参数,采样频率达10kHz。
(2)边缘计算节点:采用NVIDIA Jetson系列嵌入式设备,实现数据预处理(降噪、特征提取)和异常初筛。某风电场的边缘节点将传输数据量降低82%,同时保证97%的异常识别准确率。
网络传输层优化方案
(1)工业协议转换网关:支持Modbus、OPC UA、Profinet等协议转换,通过MQTT/CoAP协议实现跨平台通信。某汽车工厂部署的协议转换系统使设备联网率从65%提升至98%。
(2)5G+MEC融合组网:利用5G网络切片技术保障关键数据传输,结合多接入边缘计算降低时延。某钢铁企业远程操控系统端到端时延控制在15ms以内。
云端智能分析平台
(1)时序数据库集群:采用TDengine处理百万级测点的时序数据,压缩比达1:10,查询性能提升5倍。某电网公司存储300亿数据点仅需50TB空间。
(2)机器学习流水线:构建特征工程-模型训练-在线推理的自动化流程,支持LSTM、XGBoost等算法的持续迭代。某飞机制造商的预测模型迭代周期从2周缩短至3天。

设备健康度评估体系
(1)多维度健康指标:融合设备运行参数、维修记录、环境数据等建立综合评价模型。某工程机械企业构建的HI指数(Health Index)准确率达92%。
(2)故障知识图谱:整合历史维修案例、专家经验构建领域知识库,支持语义检索和推理。某半导体厂的故障诊断效率提升40%。
剩余寿命预测模型
(1)退化轨迹建模:采用Wiener过程、Gamma过程等随机过程模型描述设备退化规律。某轴承制造商实现剩余寿命预测误差<8%。
(2)迁移学习应用:利用源域设备数据加速目标设备模型训练,解决小样本问题。某水处理系统跨厂区模型迁移使训练数据需求减少70%。
维护决策优化引擎
(1)动态维护策略:基于实时健康状态和维修资源情况,自动生成最优维护计划。某化工厂设备停机时间减少35%。
(2)数字孪生仿真:构建设备虚拟镜像,模拟不同维护方案的效果。某发电集团通过仿真验证使维护成本降低28%。
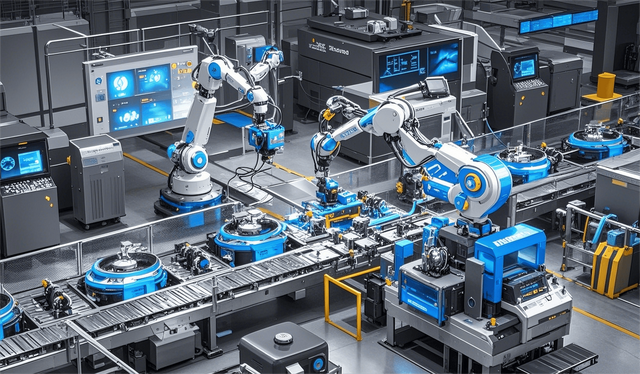
离散制造领域
某汽车零部件工厂部署的智能运维系统,集成1200台数控机床的实时监控。通过振动频谱分析和刀具磨损预测,实现:
非计划停机减少62%
刀具利用率提升45%
OEE(设备综合效率)从78%提升至89%
流程工业场景
某炼油厂构建的全厂级预测性维护平台,覆盖催化裂化、加氢处理等核心装置。采用声发射检测和红外热成像技术,实现:
关键机组故障预警提前72小时
年度检修费用降低2200万元
安全事故率下降90%
基础设施运维
某城市地铁公司应用轨道综合检测系统,集成车载传感和轨旁监测设备。通过钢轨波磨预测和接触网异常检测,达成:
轨道巡检频率降低50%
接触网故障响应时间缩短至15分钟
年度维护成本节约1800万元


当前,随着数字孪生、联邦学习等新技术的发展,设备智能运维正朝着自主决策方向演进。企业需要建立"监测-诊断-预测-决策"的闭环体系,通过持续的数据积累和模型优化,最终实现从预防性维护到预测性维护的质变跨越。建议实施方重点关注业务场景适配度,采取"试点先行、迭代优化"的实施策略,确保技术价值有效落地。