在工业 4.0 的浪潮席卷全球之际,制造业正经历着一场前所未有的深刻变革。从传统生产模式向智能化、数字化转型,已成为企业在激烈市场竞争中生存与发展的必然选择。而数字工厂,作为这场变革的核心载体,究竟在工业 4.0 中占据着怎样的战略地位?又发挥着哪些关键作用?

工业 4.0 的本质,是借助物联网(IoT)、人工智能(AI)、大数据和云计算等前沿技术,实现物理世界与数字世界的深度融合,达成生产全流程的智能化与协同化。而数字工厂,正是这一理念的具体呈现。它的核心在于构建网络物理系统(CPS),通过传感器、软件和互联设备,实现机器、流程与人之间的无缝交互。
数字工厂具有三大显著特征:一是互联互通,工厂内所有设备、系统均通过物联网连接,数据实现实时共享;二是智能决策,借助 AI 和大数据分析,系统能够自主优化生产参数并预测潜在风险;三是柔性生产,支持小批量、个性化订单的高效切换,大幅降低转换成本。罗兰贝格的研究数据极具说服力,数字工厂可为美国汽车行业每年节约成本高达 160 - 320 亿美元,同时将生产效率提升 20% 以上,这充分彰显了其在工业 4.0 中的核心地位。
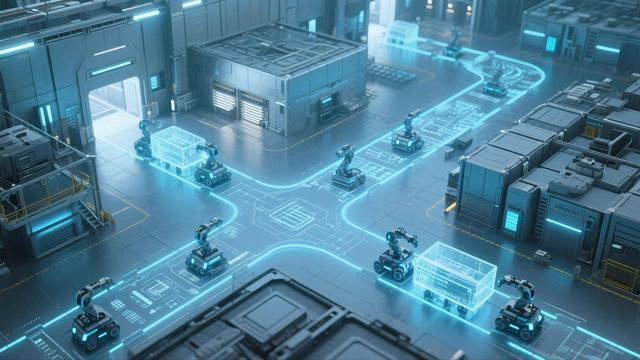
1. 制造自动化:从孤立到全局优化
在传统制造业中,自动化设备大多独立运行,彼此之间缺乏有效协同。而数字工厂借助网络物理系统(CPS),将机器、物流、库存等各个环节整合为一个统一的网络。传感器实时采集设备状态数据,云计算平台对这些数据进行分析后,动态调整生产节奏,从而实现资源的最优配置。
某生产企业通过生产性能管理软件实时监控设备数据,并结合 AI 预测维护需求,成功将设备故障率降低 30%,维护效率提升 40%。这种从孤立设备到全局优化的转变,为企业带来了显著的效益提升。
2. 预测性维护:从被动到主动
传统的设备维护主要依赖定期检修,这种方式不仅成本高昂,而且效率低下。数字工厂借助物联网传感器,实时监测设备的振动、温度等关键参数,并结合机器学习算法预测故障风险。麦肯锡的报告显示,预测性维护可降低维护成本 10 - 40%,减少停机时间 50%。
某能源企业利用智能运维系统分析发电设备数据,提前发现电机过热风险,及时采取措施,成功避免了价值数百万美元的生产中断。从被动维修到主动干预,预测性维护为企业的稳定生产提供了有力保障。
3. 智慧物流:从人工到智能协同
在新冠疫情和供应链危机的双重冲击下,物流管理成为制造业面临的一大痛点。数字工厂通过物联网追踪物料位置、优化库存路径,并结合机器人实现仓储自动化。某大型仓储中心采用的人机协作模式,将分拣效率提升了 3 倍。
数据显示,智慧物流系统可将库存周转率提高 20%,同时降低资产损失率 15%。从人工调度到智能协同,智慧物流有效提升了企业的供应链管理水平。
4. 数据驱动决策:从经验到科学
数字工厂的传感器每日会产生海量数据,但传统企业往往只能利用其中的 5%。通过云计算和大数据分析,企业能够深入挖掘数据价值,优化生产参数、能耗管理和质量控制。某制造厂商通过分析生产线数据,将产品缺陷率降低了 25%。
AI 算法能够识别复杂工艺中的异常模式,如焊接强度不足等,并实时调整设备参数,确保产品质量的一致性。从经验主义到科学管理,数据驱动决策为企业的高质量发展提供了重要支撑。
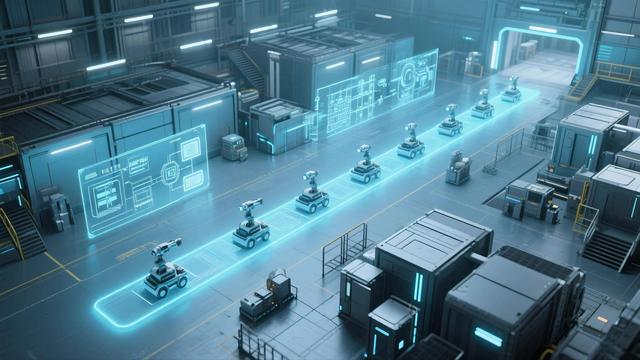
尽管数字工厂前景广阔,但在落地过程中仍面临诸多挑战。技术复杂性是一大难题,整合物联网、AI、云计算等技术,对于中小企业来说难度较大;设备互联增加了数据安全风险,网络攻击的潜在威胁不容忽视;此外,既懂工业流程又精通数字技术的复合型人才稀缺。
针对这些挑战,企业可以采取分阶段实施的策略,从局部自动化逐步扩展至全厂智能化,降低初期投入风险;强化网络安全,采用加密通信、权限管理等技术保护数据资产;加强产学研合作,联合高校与科技企业培养工业 4.0 专业人才。
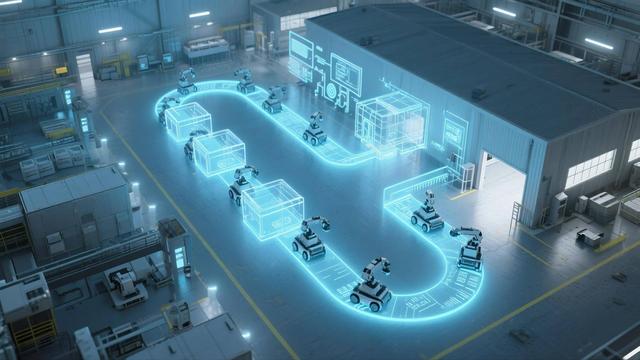
到 2030 年,数字工厂将实现全生命周期数字化,涵盖产品设计、生产规划、制造执行到售后服务的每一个环节。早期布局的企业已展现出显著优势,如某工厂通过工业 4.0 改造,生产效率提升 25%,订单交付周期缩短 50%。
对于设备管理系统而言,数字工厂的普及将催生更高的需求,全生命周期管理以及移动端协同将成为重要发展方向。
数字工厂作为工业 4.0 的核心载体,在制造业转型升级中发挥着不可替代的作用。它通过智能化、数据化的手段,帮助企业降本增效、提升竞争力。在未来的全球化竞争中,拥抱数字工厂变革、加速技术融合的企业,必将占据领先地位,书写制造业发展的新篇章。