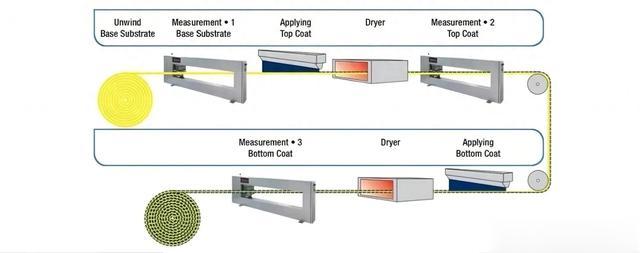
电极干燥工序的产品特性和控制点。干燥后的电极关键指标,如干燥均匀性,这直接影响到电极的一致性。如果干燥不均匀,可能会导致局部应力或者裂纹,影响电池性能。残余溶剂含量,残留过多的话,在后续工序中可能会产生气体,影响电池的安全性,或者导致电解液分解。孔隙率和结构稳定性,孔隙率影响离子传输,结构稳定性关系到电极是否容易破裂或脱落。粘结剂分布也是重点,如果粘结剂分布不均,活性材料可能脱落,影响电池寿命。厚度和面密度的一致性,这关系到电池容量和能量密度。
控制点,在干燥过程中需要监控和调整的参数。温度控制很关键,温度过高可能损坏材料,温度过低溶剂挥发不完全。干燥时间需要平衡生产效率和干燥效果。风速和风量影响溶剂蒸发速率,需要均匀分布。湿度控制同样重要,环境湿度过高会减慢干燥速度。涂布参数如初始厚度和均匀性会影响干燥结果,还有设备的清洁和维护,避免交叉污染。
一、电极干燥后的关键产品特性
干燥均匀性技术指标:极片横向/纵向溶剂残留差异(通常要求<3%)影响机理:不均匀干燥会导致活性物质颗粒间内应力差异,引发微裂纹(尤其在NCM高镍正极中更敏感),降低离子/电子传输效率。检测手段:红外热成像(IR)监测温度场分布,激光诱导击穿光谱(LIBS)分析成分均匀性。残余溶剂含量控制目标:NMP(正极)或水(部分负极)残留量<500ppm失效风险:残留溶剂在注液后与电解液(如LiPF₆)反应生成HF,加速SEI膜分解,导致产气(如CO₂、CH₄)和循环膨胀。先进工艺:采用真空阶梯干燥(如先80℃常压后120℃真空),可降低NMP沸点并提升脱出效率。孔隙率与孔径分布理想范围:正极30-40%,负极25-35%(视材料体系调整)控制逻辑:孔隙率过高→电解液浸润性好但能量密度下降;孔隙率过低→锂离子扩散受阻,倍率性能恶化。调控手段:通过干燥速率控制(如梯度升温)调节粘结剂(PVDF或SBR)迁移方向,形成垂直孔道结构。粘结剂分布与界面结合力关键问题:快速干燥易导致粘结剂向表面富集(Skin Effect),降低活性物质-集流体结合力(剥离力需>20N/m)。解决方案:引入微振荡干燥(频率5-10Hz)打乱溶剂蒸发路径,促进粘结剂均匀分布。机械强度与柔韧性测试标准:180°弯曲测试无裂纹,抗拉强度>2MPa失效案例:硅基负极因干燥收缩应力大导致极片脆化,需添加纳米纤维素(CNF)等增韧剂。二、干燥工序核心控制点及优化策略
温度场精准控制多段温区设计:初始区(50-80℃):缓慢蒸发避免表面结皮主干燥区(100-130℃):强化传质效率后稳定区(80-90℃):释放残余应力创新技术:电磁感应加热(针对铜箔集流体)可实现定向加热,能耗降低30%。风场动力学优化气流模型:采用计算流体力学(CFD)模拟优化喷嘴角度(建议15-30°倾角),确保雷诺数Re>5000实现湍流干燥。案例参考:特斯拉专利(US20210175212A1)提出螺旋式风道设计,风速均匀性提升至95%。在线闭环控制系统传感技术:太赫兹波(THz)实时监测极片含水率(精度±0.1%)微波共振法测量面密度(分辨率±0.5g/m²)控制算法:基于模型预测控制(MPC)动态调整风速/温度,应对环境湿度波动。材料适配性工艺开发高固含量浆料(如55%固含的LFP正极):需提高干燥速率(>0.5m/min)防止沉降厚电极(>200μm):采用红外辅助干燥(IR + Hot Air)增强内部传热,避免"夹生"现象。缺陷预防机制裂纹抑制:控制干燥收缩率<0.15%/s(通过调节干燥区湿度至20-30%RH)卷曲控制:双面不对称干燥技术(背面加热功率提高10-15%)补偿应力差。三、前沿技术趋势
绿色干燥技术超临界CO₂干燥(ScCO₂):替代NMP溶剂体系,干燥时间缩短50%且无VOC排放辐射干燥:采用近红外(NIR)选择性加热活性物质颗粒,能耗降低40%数字化孪生应用建立干燥动力学模型(包含Fick扩散方程和Darcy渗流定律),虚拟调试优化工艺窗口。AI驱动的工艺优化基于深度学习的缺陷预测系统(输入参数:温度曲线、风速、浆料流变数据;输出:孔隙率预测误差<2%)通过精细化控制干燥过程中的传热传质行为,可提升电极性能一致性,最终实现电池能量密度。
系统化工艺步骤和控制点
一、工艺步骤分解
1. 前处理阶段
步骤1.1 湿电极导入与定位
控制点:张力控制(50-150N,防止褶皱)纠偏精度(±1mm,避免边缘干燥不均)检测手段:激光边缘传感器+CCD视觉定位2. 预干燥区(溶剂快速挥发)
步骤2.1 表面溶剂闪蒸
控制参数:温度:60-80℃(正极用NMP时需控温≤85℃防沸腾)风速:8-12m/s(湍流模式,雷诺数Re>4000)湿度:<30%RH(防止溶剂二次吸附)目标:30秒内去除80%表面溶剂监测技术:在线红外光谱(NIR)实时反馈溶剂残留3. 主干燥区(深层溶剂脱除)
步骤3.1 梯度升温干燥
温度曲线:第一段:90℃/2min → 蒸发中间层溶剂第二段:110-130℃/3min(真空度-0.08MPa加速NMP脱出)第三段:70℃/1min(应力释放)核心逻辑:通过Darcy定律控制溶剂扩散速率(目标:扩散系数>1×10⁻⁹ m²/s)步骤3.2 风场协同优化
气流设计:喷嘴角度:20-35°(冲击干燥效率最大化)风压分布:极片上下表面压差<50Pa(防卷曲)创新方案:特斯拉专利风刀系统(风速均匀性>95%)4. 后处理与质量闭环
步骤4.1 在线缺陷检测
检测项:裂纹:线阵相机+AI图像分析(灵敏度10μm)厚度波动:β射线测厚仪(精度±1μm)处置机制:实时标记缺陷位置,联动MES系统自动分拣步骤4.2 终检与收卷
关键参数:残余溶剂:GC-MS检测(目标<300ppm)剥离强度:90°剥离测试仪(>25N/m)卷曲度:激光测距仪(翘曲高度<2mm/m)二、关键控制点(CP)与过程能力指数(CPK)
控制点
参数范围
监测频率
CPK目标
失效模式
干燥温度均匀性
±1.5℃以内
每15分钟
≥1.67
局部过烘导致粘结剂失效
面密度一致性
±1.5g/m²(3σ)
连续在线
≥1.33
电池容量跳水
孔隙率分布
32-38%±2%(正极)
每批次
≥1.50
锂枝晶生长风险
残余应力
<5MPa(DIC数字图像相关法)
每4小时
-
极片分切时微裂纹扩展
三、工艺异常处理逻辑
1. 溶剂残留超标(>500ppm)根因分析:温度曲线与浆料固含量不匹配(高固含量需延长高温段)真空系统泄漏(真空度下降>10%)对策:动态调整干燥时间:ΔT= (实测残留量 - 目标值)/50ppm × 10秒启用备用真空泵并校准密封件2. 极片横向裂纹
机理:干燥速率梯度>0.2%/s导致应力集中解决方案:调节湿度:从20%RH升至40%RH减缓蒸发速率增加微振动模块(振幅50-100μm,频率20Hz)释放应力3. 面密度波动(±3g/m²)
补偿算法:前馈控制:基于浆料粘度(Brookfield值)预测干燥收缩率反馈控制:根据β射线实测值调整涂布头开度四、数字化工艺管理架构
数据采集层:集成温度/湿度/张力传感器(采样率≥10Hz)光谱仪+机器视觉数据流(带宽>1Gbps)分析层:建立干燥动力学数字孪生模型(COMSOL多物理场耦合)基于PCA主成分分析识别关键变异源执行层:边缘计算实时调控(响应时间<200ms)自动生成SPC报告(Cp/Cpk, PPK, 西格玛水平)五、进阶工艺路线
2024技术突破:脉冲式微波干燥(2.45GHz):穿透加热极片内部,干燥时间缩短40%量子点温度传感:纳米级温度分辨率(0.01℃)防止局部过热通过上述系统化控制,可将电极干燥工序的OEE(设备综合效率)从65%提升至85%以上,同时降低能耗成本30%。建议结合DOE实验设计优化参数组合,实现六西格玛级工艺管控。