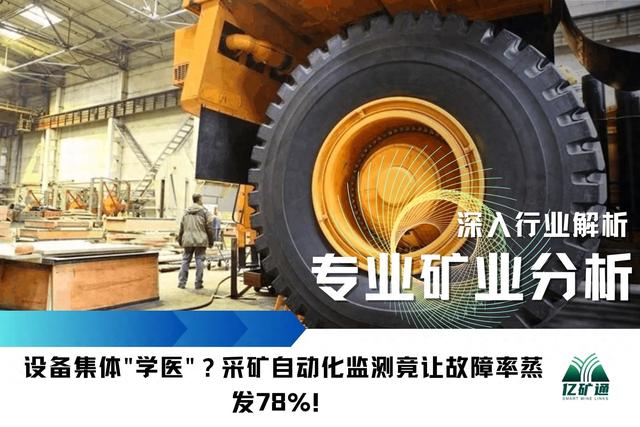
在机械轰鸣的矿山深处,一场静默的"数字医疗革命"正悄然上演。
当传送带轴承开始自主"号脉",破碎机齿轮学会"体温报警",传统采矿业的设备管理逻辑被彻底颠覆。
这场由自动化监测技术主导的变革,正在将"故障维修"变成考古学词汇。
嵌入式传感器构成的"数字经络系统",让每台设备都拥有了实时健康档案。
在智利某铜矿的皮带运输系统中,278个监测点持续上传振动频谱数据,云计算平台通过对比5000+正常工况模型,准确捕捉到0.03毫米级的轴心偏移。
这种纳米级感知能力,使预防性维护响应速度提升至传统人工巡检的23倍。
AI诊断引擎犹如设备专属"全科医生",在数据洪流中精准定位病灶。
某铁矿的智能监测系统,通过分析破碎机12年的声纹数据库,成功预警16次衬板裂纹事故,最惊人案例提前54小时锁定故障位置。
这种预测能力不仅减少83%的非计划停机,更让关键部件使用寿命延长至原设计标准的132%。
无人机舰队正在接管矿区的"空中急诊科"。
搭载热成像与激光雷达的自主飞行单元,仅需2.3小时即可完成40公顷露天矿场的全面扫描。
在澳大利亚某锂矿,无人机群发现输送带支架的0.5℃异常温升,及时避免可能引发连环停机的结构性坍塌。
相比人工检测,这种空中监测体系将高危区域检查效率提升47倍。
数字孪生构建的"平行医疗空间",让设备在虚拟世界先"死"一次。
某重型矿卡制造商通过1:1三维模型,在数字环境中模拟出2700种极端工况,提前3个月预判出液压系统设计缺陷。
这种虚实联动的"预诊断"模式,使实际运营中的突发故障降低71%,维护成本曲线呈现反常规下降趋势。
这场技术革命正在重构采矿业的成本方程式:
某金矿中央控制室的42块屏幕上,跳动着全球8个矿区的16万组实时数据
智能诊断系统每年自动生成3800份设备"体检报告",合规审查时间压缩92%
预测性维护体系使单台旋回破碎机年度维护成本从180万元降至67万元
设备全生命周期管理平台让资产利用率提升至89%的历史峰值
但智能监测的"数字乌托邦"仍面临现实裂缝:
某铜矿的无线传感网络曾因井下电磁干扰出现17%数据失真
AI模型在应对新型复合材料磨损预警时出现26%误判率
跨国矿企每年需投入2.7%营收用于维持监测系统的网络安全
当边缘计算节点开始承担80%的本地决策,当区块链存证为每份诊断报告加上"数字指纹",采矿业的设备健康管理正进化出自主神经系统。
在刚果(金)某钴矿,具备自学习能力的监测系统,已在没有工程师干预的情况下,自主优化了13项设备运行参数。
这场变革的本质,是将采矿设备从冰冷钢铁转化为数据生命体。
每个振动频率都是设备的心跳,每次温度波动都是钢铁的呼吸,而自动化监测系统正扮演着数字时代的"设备医者"。
当预防性维护进化成预测性干预,当故障维修转变为参数微调,采矿业终于触摸到了"零意外停机"的圣杯边缘。
诚邀参与:共筑智矿 携手转型值此关键节点,新疆维吾尔自治区应急管理厅指导,中国安全生产协会、中国矿业大学、新疆工程学院和新疆矿山智能化产业联合会联合主办的“2025智能矿山发展大会(新疆)”将于2025年5月16日-18日在新疆昌吉亚欧国际会议中心隆重举办。大会以“科技进疆 智矿慧企”为主题,汇聚全国100+煤矿和露天煤矿无人驾驶安全运营标准非煤矿山企业、数十位权威院士专家、产业链上下游领军企业,共同探索智能化矿山建设的进阶路径与创新生态。同时,大会将重点发布《2025智能矿山暨无人驾驶行业蓝皮书》,系统梳理无人驾驶、智能分选等技术的应用图谱与行业趋势,并首次披露《矿山无人驾驶安全运营标准》《非煤矿山智能化建设标准》编制工作最新进展。
2025智能矿山发展大会(新疆)组委会期待您的参与,共同推动矿业智能化发展新篇章。
THE END
编辑 | 全球智慧矿业创新研究院
组织 | 智慧矿业专业委员会
运营 | 亿矿通
❖免责声明:所载内容来源网络、微信公众号等公开渠道,转载稿件版权归原作者、机构所有,转载仅供参考、交流等非商业目的,如有侵权,请联系我们删除。
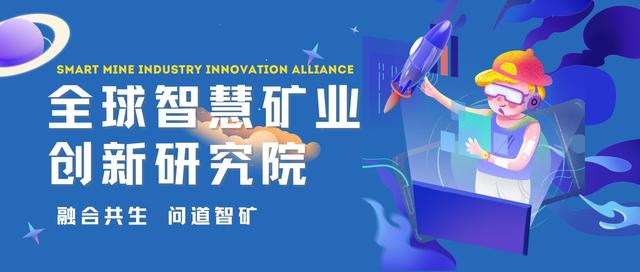