螺纹元件具有灵活的安装位置、标准化的结构设计、功能的多样性,是螺杆挤出机内使用最多的部件。
本文采用有限元软件,研究了高黏聚合物在常规螺纹元件、开槽螺纹元件和啮合块3种螺纹元件中的流场特征,分析了不同流体参数对3种螺纹元件混合性能的影响。
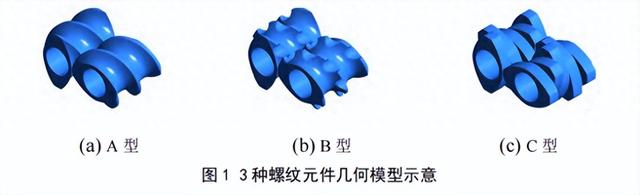
为了便于计算,模拟工况简化如下:
1)混合过程中聚合物熔体的密度保持不变;
2)忽略熔体的湍流流动,仅考虑层流流动;
3)忽略重力、惯性力等体积力;
4)熔体在流道中是完全充满的状态。
有限元模型:利用前处理软件分别对流场和螺纹元件进行网格划分,如图2和图3所示。
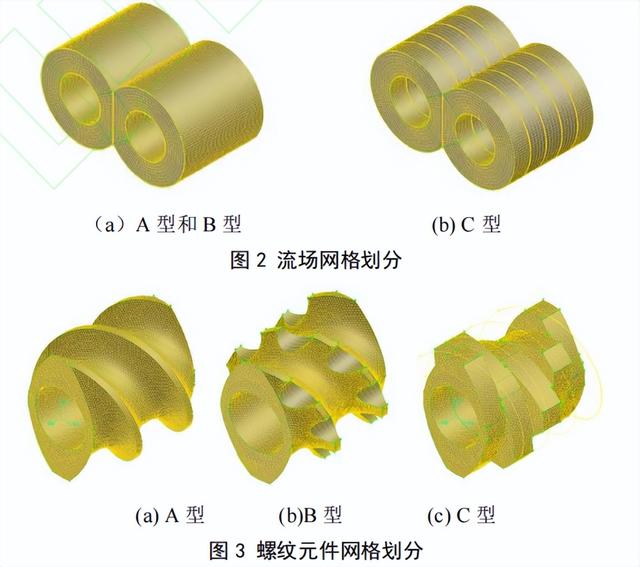
聚合物流场边界条件:流场出入口均为自然流动状态(fn=fs=0),左右螺杆转速均为300r/min,机筒内表面无相对运动。
01螺纹元件的流场压力

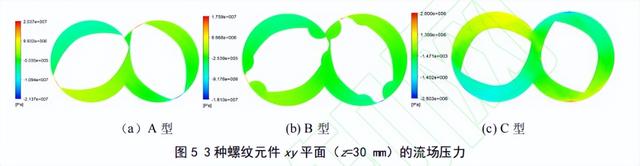
由图4可以看出:
沿双螺杆挤出机旋转方向,靠近流场出口一侧压力较大,整个流场最高压力位于螺纹元件与螺纹元件的啮合区域;由于聚合物为非牛顿幂律流体,随着螺棱的推进作用,熔体压力会突然变大,离开螺棱后压力逐渐降低,总体趋势是:从入口到出口,压力逐渐递增,这是因为在挤压过程中,熔体在螺棱处受到较大推进力,离开螺棱时挤压力降低,但流场压力随熔体不断混合、压实而逐渐升高。
另外,3种螺纹元件流场的出口压力均大于入口,且压力梯度变化较明显,说明3种螺纹元件均具有建压能力。B型外壁面设计8个螺旋均布的沟槽,导致物料在通过内部腔体时出现明显的漏流和混流现象。因此,B型压力场变化较小,速度场变化较大,局部剪切速率变化较小。
流场峰值压力:A型>B型>C型。
02螺纹元件局部剪切速率
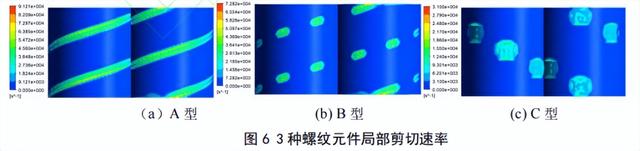
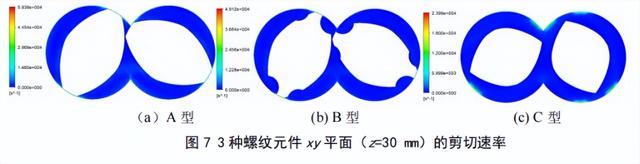
由图6和图7可以看出:
高剪切应力主要集中在2个螺纹元件的啮合区及螺纹元件与筒体内壁之间。
沿挤出方向,A型局部剪切速率峰值最大,B型次之,C型最小。
03螺纹元件平面的熔体速度
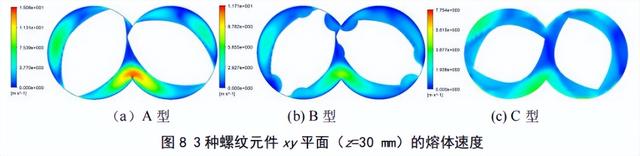
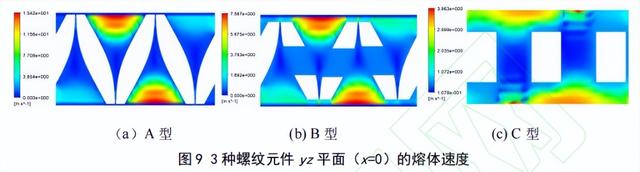
由图8和图9可以看出:
3种螺纹元件在靠近螺棱的速度均相对较大,且在啮合区域熔体速度均会突然增大。在靠近筒体中心位置,熔体有明显的回流现象,有利于熔体充分混合。
熔体速度性能:A型>B型>C型。
04流变参数对混合性能的影响
选取典型的A型,分析不同流变参数对混合性能的影响。图10为A型模型取样点,其中,箭头为挤出方向,A点和B点为取样点。图11为A型的参数分析。

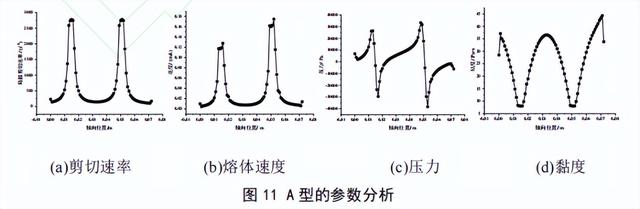
由图11(a)可以看出:局部剪切速率随螺棱及螺棱支撑面的位置而不断变化,接近螺棱处时急剧増大,整个流场区域的入口和出口处局部剪切速率最小。第一个螺棱支撑面处的局部剪切速率超过2 750 s-1,沟槽位置(轴向位置为3 cm)局部剪切速率值最小,趋于0。
由图11(b)可以看出:当螺杆将物料输送至入口一侧时,熔体速度较小,随着混合程度的进行,熔体速度缓慢增大,在第一个螺棱处(z=0.015 m)超过0.12 m/s,通过第一个螺棱后又迅速下降,这是因为物料在双螺杆挤出机内部不断螺旋输送前进,物料受到两螺杆之间的摩擦力,熔体速度迅速降低,当其趋于0时,基本保持稳定。当物料到达第二个螺棱(z=0.05m)时,熔体速度迅速升至0.17 m/s,然后又迅速下降,并趋于稳定。
如图11(c)所示:挤出过程中压力变化特性上述已描述,压力的变化趋势与局部剪切速率和熔体速度的变化相近,即三者呈正相关,即压力增大时,剪切速率和熔体速度均呈现增大的趋势。
剪切应力随剪切速率增加而增大,而黏度却与前两者成反比。由图11(d)可以看出:剪切速率的变化趋势与黏度的变化趋势相反,当剪切速率减小时,黏度分布处于增大趋势,反之亦然。
试验验证

图12为PP熔体在3种螺纹元件中的流动状态,其中,螺杆转速为300 r/min。由图12可以看出:PP熔体在3种螺纹元件中均实现平推流,且筒体内壁及螺纹元件上基本没有大块物料附着,说明3种螺纹元件均具有较好的自清洁性能,表现出较好的混合效果和剪切效果。A型的剪切能力最好,B型次之,C型最弱。
在试验初期,设计的螺杆组合只包含螺纹元件和啮合块,但整个反应的混合性较好,熔体在筒体内部的充满度较高,但返混能力弱。
后期通过模拟分析,对螺纹元件位置进行调整,在啮合块靠近喂料端一侧增加了开槽螺纹元件,整个流场的返混能力得到改善。
同时,开槽螺纹元件建压能力和输送能力弱,物料在内部流场的充满度高,停留时间会延长。试验验证结果与仿真模拟结果具有较高的一致性。此外,螺杆长径比由52∶1缩小为44∶1。