在中国新材料产业版图中,光威集团的名字与“碳纤维”紧密相连。这家以渔具制造起家的民营企业,用30余年时间完成了一次令人惊叹的产业跃迁——从生产碳纤维钓鱼竿的“小作坊”,蜕变为中国高端碳纤维国产化的领军者,甚至跻身军工供应链。这一历程不仅是中国制造自主创新的缩影,更折射出中国新材料产业突破技术封锁、实现军民融合的战略路径。

一、渔具起家
光威集团的前身是1987年成立于山东威海的乡镇企业,初期以玻璃纤维钓鱼竿为主营业务。1998年,光威创始人陈光威敏锐捕捉到碳纤维材料的潜力:这种重量仅为钢的1/4、强度却高出7倍的新材料,在海外已用于高端渔具制造。然而,当时中国碳纤维产业几近空白,国际巨头(如日本东丽)垄断全球90%以上的产能,并对中国实施严格技术封锁。
光威选择了一条“反向突围”路径——从下游应用倒逼技术研发。起初,光威面临着资金短缺和生产设备匮乏的严峻挑战。然而,在陈光威的带领下,技术骨干们连续奋战150多个日夜,终于于2002年研制出首条国产鱼竿生产线,实现了自主保障生产装备的目标。光威虽未触及碳纤维核心制备技术,但积累了关键的应用开发经验,为后续向上游延伸埋下伏笔。这一突破不仅标志着光威正式进军钓具产业,更为后续的发展奠定了坚实的基础。凭借自主研发和持续创新,光威鱼竿逐渐在市场上崭露头角,并以其高性能和优质品质赢得了国内外消费者的青睐。
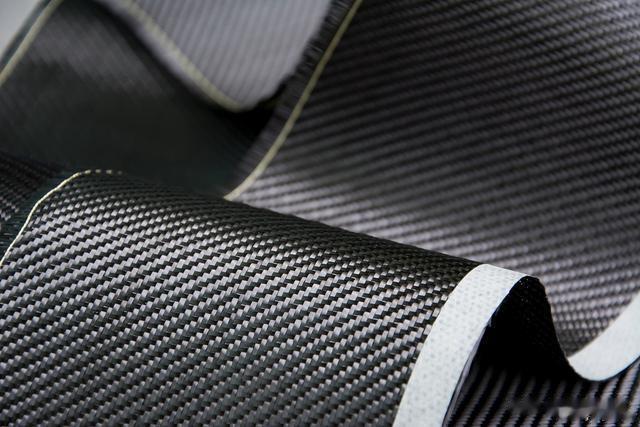
二、逆流而上:突破碳纤维“卡脖子”技术
碳纤维产业链的核心壁垒在于原丝制备和碳化工艺。原丝质量直接决定最终产品性能,而中国长期受困于“缺芯少丝”——高端碳纤维原丝依赖进口,军用领域更被禁运。
经过数年的努力,光威启动碳纤维自主研发,成立威海拓展纤维有限公司,终于在2005年主攻T300级(军工基础级)碳纤维。一举打破了国外垄断,填补了国内碳纤维事业的空白。这一成果不仅为航空航天和国民经济高技术领域急需的碳纤维提供了技术和条件支持,更为光威在碳纤维领域的深入发展奠定了坚实的基础。
2007年,光威建成国内首条千吨级碳纤维生产线,打破国外垄断,产品通过军方验证,成为我国首个军用碳纤维供应商。
2012-2017年,光威攻克T700、T800级高强中模碳纤维技术,并实现M40J高模碳纤维工程化,产品应用于卫星、导弹等尖端领域。
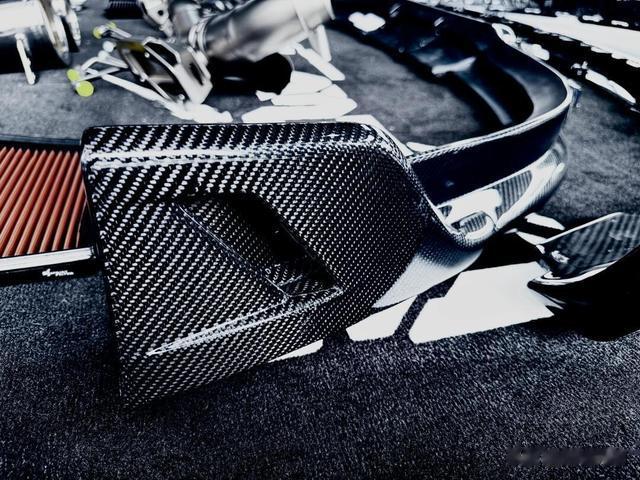
光威的突破标志着中国碳纤维从“能用”走向“好用”。其自主研发的GQ3522(T300级)碳纤维被列入国家863计划成果,支撑了多型武器装备减重增效需求,直接助力国防装备升级。
三、全产业链布局:军民融合的生态构建
为摆脱对单一军工订单的依赖,光威开启“军技民用”的产业化扩张:
光威构建“原丝-碳化-复合材料-终端制品”全链条,2021年建成万吨级碳纤维生产基地,覆盖航空航天、风电叶片、汽车轻量化等多领域。
光威 通过旗下上市公司光威复材(300699.SZ)对接资本市场,募集资金投入高端碳纤维及复合材料研发。
光威 2023年发布T1100级超高强碳纤维,对标国际顶尖水平,并布局大丝束碳纤维(48K以上)量产,降低工业级应用成本。

四、挑战与启示:中国碳纤维产业的突围密码
光威的崛起背后,是中国新材料产业发展的典型逻辑, 以军工需求为突破口,通过国家项目支持实现技术积累,再向民用市场释放产能。 从下游制品反向攻克上游技术,规避了“实验室到市场”的鸿沟。单一技术突破难以形成护城河,全产业链控制力才是长期优势所在。尽管光威已跻身全球碳纤维产能前十,但与国际巨头相比,其在高端产品稳定性、成本控制方面仍有差距。日本东丽等企业凭借数十年技术沉淀,仍主导着航空级碳纤维市场。此外,全球碳纤维产能过剩风险隐现,如何平衡军民品结构、开拓新应用场景,将是光威下一阶段的关键命题。
总之,从渔竿车间到军工重器,光威的历程印证了一个真理:核心技术靠化缘要不来,唯有自主创新。在中国制造向高端跃迁的今天,光威的故事不仅是一家企业的奋斗史,更是一面镜子——照见中国产业升级的艰难与荣耀,也映射出新材料领域“国产替代”的深远意义。