一、纤维复合材料概述
新材料的重要发展方向:
材料复合化:1+1>2
复合材料:“取长补短”、“协同作用”。
由两种或两种以上物理和化学性质不同的材料复合而成的新材料,它既能保留原组成材料的主要特征,还能通过复合效应获得原组分所不具备的性能。
复合材料及其优势
Fibre/纤维
▪ 决定复合材料的强度和刚度。
▪ 影响复合材料抗变形和抗疲劳能力,导电性,传热性。
Resin/树脂
▪ 粘合纤维,使复合材料能够承担剪切和压缩载荷。
▪ 决定复合材料的成型工艺和使用温度。
▪ 影响复合材料的某些性能。
▪ 影响材料抵抗环境变化,抗变形和抗疲劳性能。
碳纤维与环氧树脂等关键基础材料的品质控制是影响复合材料综合性能的重中之重!
从源头抓起,做好基础材料,提升复合材料品质!
二、环氧树脂在复合材料中的优势及应用
纤维复合材料的优势
1、低密度,高的比强度、比刚度
2、高设计灵活性
3、优异的耐腐蚀能力
4、易于整体成型,降低装配成本
5、尺寸稳定性好

表1 典型树脂基复合材料和金属材料性能
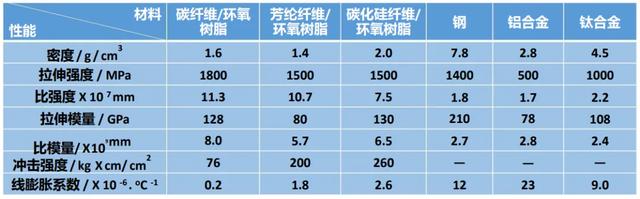
复合材料的性能可设计性
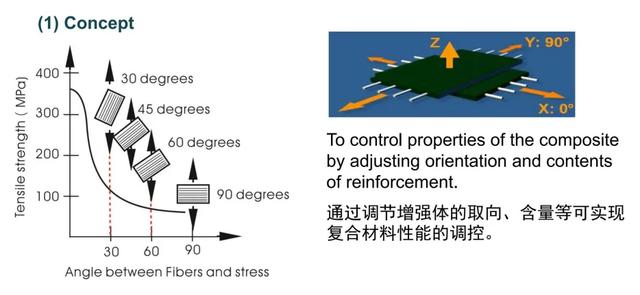
复合材料成型工艺

各种成型工艺对树脂粘度的要求
• 缠绕 : 600 cPs以下,最好300~500 cPs
• 拉挤: 800~1200 cPs
• 真空导入:300 cPs以下,200 cPs左右
• 预浸料: 10000~50000 cPs
工艺性:树脂是关键!
预浸料的优势
1、最大强度特性。典型的手工铺层会有大量过量的树脂,过量的树脂会增加脆性并降低整体性能。而预浸料能够精确控制纤维和树脂含量,这是实现最大固化性能的理想选择,通常在常规的手工层压中是无法实现的。
2、均匀性和可重复性。预浸料厚度均匀,并且从模具中出来的每个零件在理论上都可能是相同的。
• 复合材料的性能很大程度上取决于预浸料的性能:
▶对复合材料结构设计师而言,预浸料是具有一定力学性能的结构单元,可用以进行结构设计;
▶对复合材料工艺工程师而言,预浸料是制造结构的原料,可以直接用以制造各种复合材料结构件。
▶预浸料的优劣关系到复合材料的质量,因此,预浸料对复合材料的应用和发展具有重要意义。
预浸料生产线:
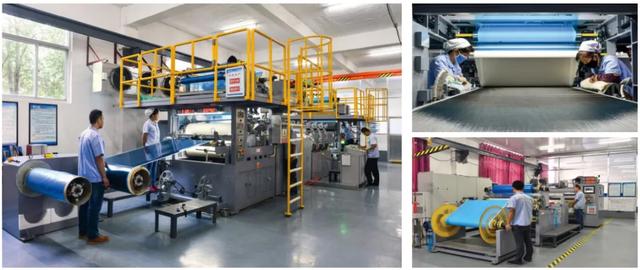
预浸料对树脂的要求
• 力学性能:强度、模量、韧性…
• 工艺性能:成型温度低,压力小,时间段,预浸料加压带宽,适于共固化成型,适于零吸胶工艺,黏度适中,铺覆性好,挥发分低,对人体无害。
• 耐热性:玻璃化温度适当高,湿热性好。
• 耐环境性能:对水、化学药品、油类、紫外线等的抗耐性能良好。
• 功能性:导电性、导热率、透波性、阻燃性(低烟、低毒、低热释放速率)
• 储存性能:储存寿命长。
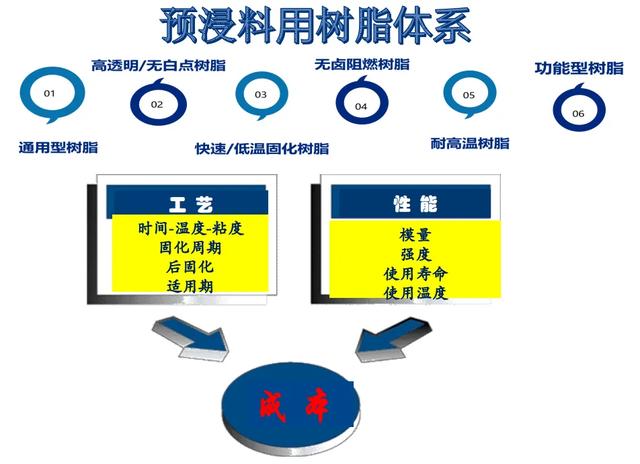
环氧树脂预浸料发展方向
1、开发高韧性防弹预浸料
2、开发阻燃预浸料
3、开发低介电预浸料
4、开发快速固化预浸料
5、开发低温固化预浸料
6、开发非热压罐(OoA)固化预浸料
历时8年,自主研发FRD树脂体系

预浸料用树脂体系--FRD
FRD-YG树脂,中温固化,刚性和韧性的完美结合。
FRD-YZ树脂,高强高韧,耐热和耐冲击性与碳纤维的匹配性好。
FRD-YGM树脂,优良的浸润性,与高模量碳纤维具有良好的匹配性,适用于低树脂含量预浸料或超薄预浸料。
FRD-YZS树脂,增强制品吸收冲击能量的同时,提高树脂和纤维的结合性。
FRD-YB树脂,优秀的无白点耐黄变特性,高浸润性,更适用于编织布预浸料。
FRD-YTM树脂,主要应用于对制品透光性有要求的场合。
FRD-Q5树脂,保证良好力学性能的前提下,150℃下5~10分钟固化。
FRD-Q20树脂,实现130℃下20分钟完成固化。
FRD-YL90树脂,90℃下完成固化,良好的力学性能,广泛应用于汽车、风电、轨道交通、船舶等领域。
FRD-YZR树脂,优良的浸润性,良好的力学性能,优异的阻燃性能。满足轨道交通、3C电子等领域的应用。
(在此基础上,衍生出低温固化阻燃预浸料用树脂体系FRD-YL-ZR树脂,轻量化阻燃树脂体FRDYQ-ZR树脂,快速固化阻燃预浸料用树脂体系FRD-YK-ZR树脂。)
FRD-Y160树脂,FRD-Y170树脂, FRD-Y180树脂, FRD-Y200树脂,良好的机械性能,高浸润性,满足客户不同温度梯度要求。
低卤环氧树脂树脂体系: 采用高纯度的环氧树脂原材料,满足以3C领域为代表的客户的需求。
三、预浸料性能表征
预浸料性能表征
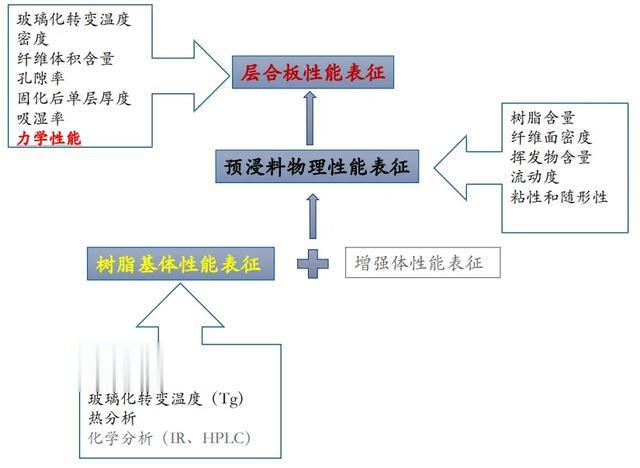
树脂基体性能表征
流变性能
▶流变性是表征未固化树脂在不同温度/时间条件下的流动性能。
▶未固化树脂的粘度通常是由流变仪测得的,将少量树脂放在两个平板之间,加热,施加一定的扭力。
▶在加热过程中,树脂内部有两种相对的力量:
① 物理因素:随着温度上升,分子链的活动性增大,导致粘度下降;
② 化学因素: 随着温度上升,树脂开始反应,分子链增大,导致粘度上升。
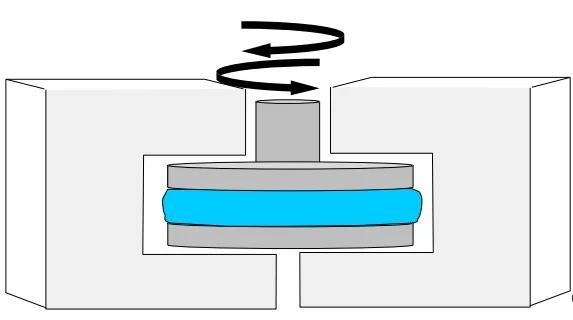
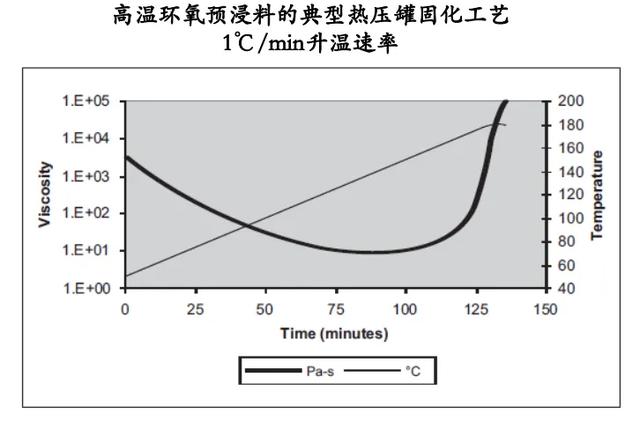
通过模拟固化工艺,可以得到粘度随温度的变化,根据实际制品的尺寸及结构选择合适的固化工艺。
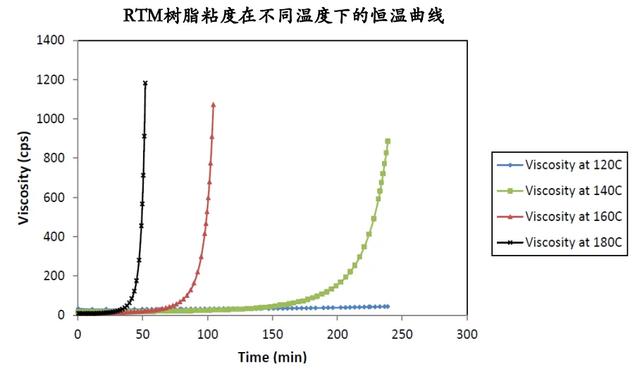
粘度计
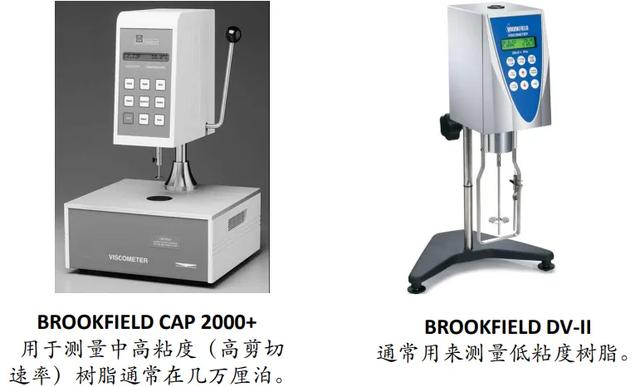
粘度计是测量树脂点粘度最主要的工具,快速且低成本的特点使其在实际研发和生产中具有广泛的应用。
凝胶时间
▶凝胶 –树脂从液体开始形成“果冻”状态,是树脂开始形成三维网状结构。
▶凝胶时间取决于:
— 测试方法
— 温度
—操作人员
▶测试方法
a. 对于树脂,将少量样品通过盖玻片放在一持续加热的平台上,牙签测探是否凝胶(拔丝);对于预浸料,在一个持续加热的平台上,将少量样品夹在两个盖玻片之间,牙签测探是否凝胶(滑动)。
b. 流变仪法:样品放在流变仪的平板之间,升温至设定温度,当储能模量和损耗模量相等时判定为凝胶点。
凝胶时间测试方法简单,但受环境、测试温度、人为操作影响较大,环境控制、测试温度的测量及规范的操作是关键。
玻璃化转变温度(Tg)
▶树脂固化后的Tg表示材料从脆性的玻璃态转变为具有一定韧性的高弹态时的温度。
▶此时整个交联结构虽然不变,但分子链段已不在固定,开始活跃起来。
▶Tg决定了最终复合材料的使用上限温度,在这个温度点附近材料的力学性能显示出明显的下降。
▶由于大多出热固性树脂都会吸湿,这会严重降低Tg,因此实际材料的使用温度应该比湿态Tg低大约30℃。
▶玻璃化转变温度的测试有好几种方法,如差示扫描量热仪(DSC)、热机械分析(TMA)、动态力学分析(DMA),由于这几种方法是测量树脂不同的性能,因此每种方法都会有不同的结果。
Tg是复合材料使用的重要参数,因此玻璃化转变温度的表征成了研发和生产的重要工作之一。
玻璃化转变温度(Tg)
典型的 DMA 曲线
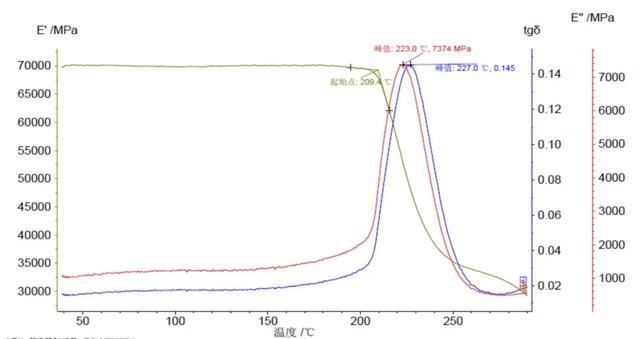
曲线显示了储能模量E’, 损耗模量E’’和损耗因子。
玻璃化转变温度(Tg)
DSC测试方法
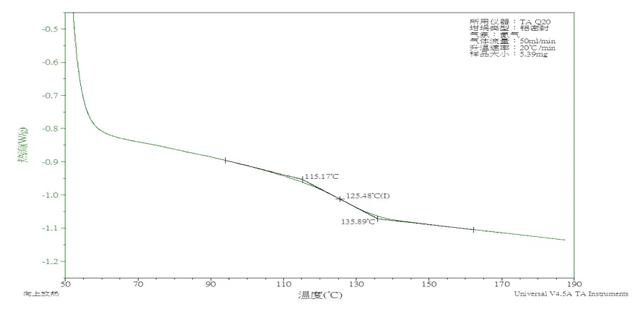
预浸料物理性能表征
定义
➢ 纤维面密度(FAW– Fiber Areal Weight ):单位面积上纤维的质量。
➢ 树脂含量(RC– Resin Content):预浸料中树脂的质量分数。
➢ 挥发份(Volatiles):预浸料中水汽、溶剂、反应副产物等小分子挥发物含量。
➢ 流动度(Flow):预浸料在加热时,树脂流动的难易程度。
➢ 粘性(Tack):预浸料在一定温度下的和模具或预浸料的粘附性。
➢ 随形性(Drape):预浸料能够铺贴成一定形状的难易程度。
预浸料物理性能的表征对客户非常重要。
层合板性能表征
层压板性能表征的内容
➢ 层压板物理性能
➢纤维体积含量
➢密度
➢固化后单层厚度
➢热膨胀系数
➢孔隙率
➢玻璃化转变温度
➢无损检测(超声扫描)
➢层压板力学性能(单层级和部分元件级)
➢拉伸
➢压缩
➢剪切(面内剪切和层剪剪切)
➢弯曲
➢开孔拉伸和压缩
➢冲击后压缩
➢螺栓挤压
层压板性能表征是整个预浸料性能表征的关键和核心。
力学性能测试
力学性能测试列表(部分)
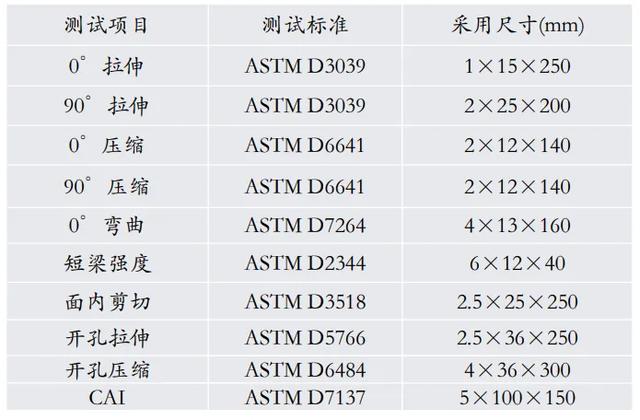
➢ 室温干态(RTD)和低温干态(CTD)的拉伸强度(Xt),主要取决于所用碳纤维,与树脂关系不大;
➢ 室温干态(RTD)拉伸模量(E1t),主要取决于所用碳纤维,与树脂关系不大;
➢ 室温干态(RTD)和高温湿态(ETW)压缩强度(Xc),与所用碳纤维和树脂均有一定关系;
➢ 室温干态(RTD)压缩模量(E1c),与所用碳纤维和树脂均有一定关系;
➢ 室温干态(RTD)和高温湿态(ETW)剪切强度(S),主要取决于树脂及其与纤维的相容性;
➢ 室温干态(RTD)剪切模量(G12),主要取决于树脂及其与纤维的相容性;
➢ 室温干态(RTD)和低温干态(CTD)的开孔拉伸强度(OHT),主要取决于所用碳纤维,与树脂关系不大;
➢ 室温干态(RTD)和高温湿态(ETW)开孔压缩强度(OHC),树脂及其与纤维的相容性起主要作用;
➢ 室温干态(RTD)和高温湿态(ETW)挤压强度,树脂及其与纤维的相容性起主要作用;
➢ 室温干态冲击后压缩强度(CAI),该指标对用于主结构的高温固化复合材料适用,但国内对用于次要薄蒙皮结构的中温固化复合材料也关心。
以上10项性能指标中:
➢ 低温干态和室温拉伸(Xt和E1t)和开孔拉伸性能(OHT)一般只与碳纤维有关,树脂影响很小,其差别只体现碳纤维性能的不同,与树脂关系不大;
➢ 压缩、开孔压缩及冲击后压缩性能与碳纤维和树脂均有关,而剪切性能主要与树脂性能有关;
➢ 评价预浸料性能的主要标志是湿热条件(ETW)下的性能与室温干态(RTD)性能之比,即所谓的性能保持率;
➢ 对所有的预浸料特别是高温固化韧性环氧树脂预浸料最关键的性能是冲击后压缩性能(CAI)。
开拓创新
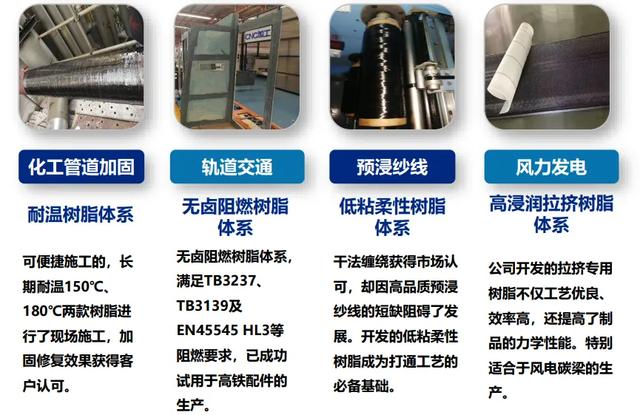
干法缠绕预浸纱线
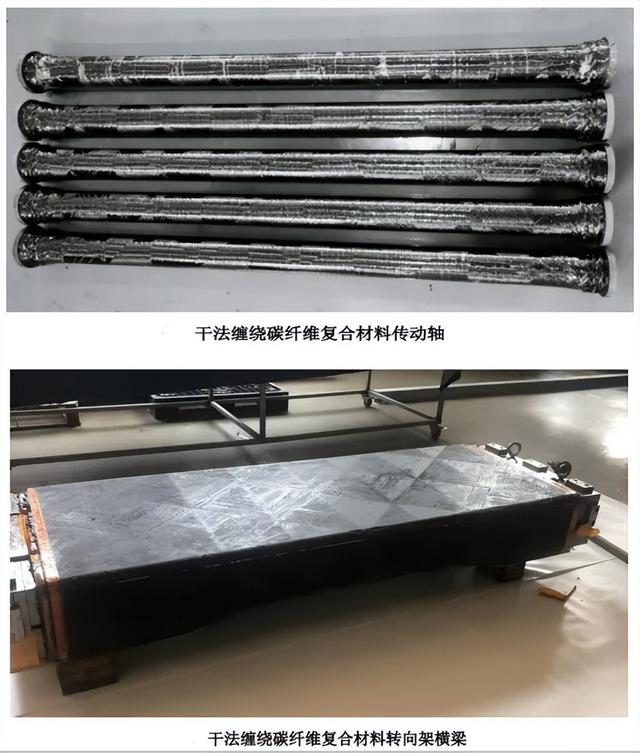
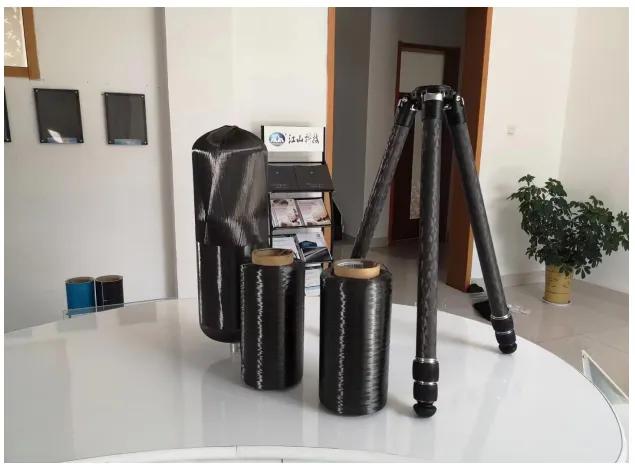
文章来源:玻纤复材
注:本站转载的文章大部分收集于互联网,文章版权归原作者及原出处所有。文中观点仅供分享交流,如涉及版权等问题,请您告知,我将及时处理!