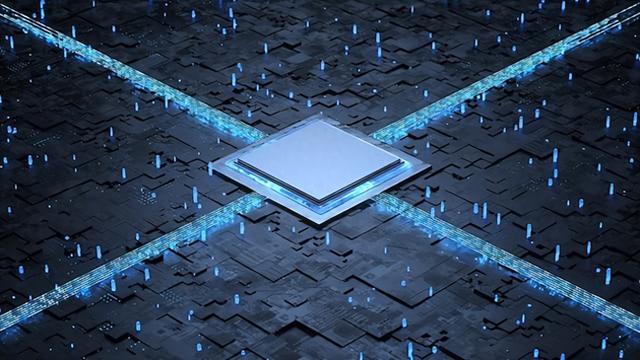
实现更好的工艺缩放和电源效率,代价是晶圆减薄、键合和先进调试等新工艺的成本。
背面供电(Backside Power Delivery, BPD)被称为游戏规则改变者 — 因其是一项突破性技术,也是 CMOS 缩放的下一个重要推动者。
BPD有望显著提升功率、性能、面积(PPA)表现,包括更快的开关速度、更低的电压下降(Voltage Droop)和更低的电源噪声。尽管极端晶圆减薄、晶圆键合及正面多层工艺堆叠导致光刻图形畸变,对前端工艺造成重大干扰,但其仍有望在2纳米以下工艺节点实现这些优势。
尽管挑战重重,但顶尖的晶圆代工厂仍稳步前行。比如,英特尔目前正在利用其 PowerVia 技术提高其 18A 节点的良率。台积电预计将于 2026 年在其 N16 节点上为 HPC(高性能计算) 应用实施其 Super Power Rail(超级电源轨道)技术。三星正在研究 BPDN 技术,尽管它尚未透露生产时间表。
背面供电技术将电源布线转移至晶圆背面,仅通过正面互连传输信号。其核心理念是直接将电力输送至所需位置。
“我们的目标是为晶体管提供更优质的电力,”imec高级研究员、研发副总裁兼3D系统集成项目总监Eric Beyne表示,“相较于通过后端15层金属堆叠以瀑布式高阻抗、高电阻损耗的方式供电,我们将电源置于晶体管下方近距离处。这能更高效地解耦前端器件。”
电源网络与数据网络的巧妙分离尤其有利于高性能计算(HPC)设备。随着制程节点的推进,寄生电压(IR)下降问题日益严重,导致性能大幅降低。背面供电网络(BPDN)通过背面更粗、电阻更低的线路供电(而非低效的正面方案),可将电压降噪相关的功耗损失减少高达30%。硅正面互连仅用于信号布线,甚至可能因减少昂贵的极紫外(EUV)光刻步骤而降低成本。
“仅仅使用反向电源有很大的成本效益,因为成本的最大驱动因素是光刻通道,”英特尔副总裁兼互连和内存技术集成总监 Kevin Fischer 说。“若突破线距极限,则需从193纳米浸没式光刻转向EUV,或从EUV转向间距倍增方案。我们在正面全部采用直接印刷,无需间距分割,即所有层的沟槽和通孔均只需一次光刻。背面仍需增加金属层,但它们是数百纳米厚的粗金属线,因此成本较低。”
然而,背面供电技术为晶圆厂引入了全新设备,例如将硅晶圆大幅减薄(至<100纳米)的研磨系统及晶圆键合系统。“涉及大量新设备,如晶圆键合与研磨,这在半导体行业并不常见,”Fischer表示,“此外还需进行正背面对准,这些都是前所未有的工艺。”
除了掌握这些新工艺外,背面供电技术还引入了必须管理的全新应力分布。例如,背面金属化和硅通孔(TSV)中不同材料的热膨胀失配会产生机械应力,可能影响晶体管特性。Lam Research的Semiverse Solutions团队通过虚拟制造研究发现,相较于传统正面连接方案,背面直连方案会对全环绕栅晶体管施加显著的额外应力。
转向背面供电对设计和制造均产生重大影响。“一大优势是释放了原本被电源占用的布线资源,”Synopsys高级产品经理Jim Schultz表示,“但充分利用这些额外的信号布线需要EDA工具的大量重构,因为过去几十年的方法一直是同时优化电源与信号布线效率。这是一次重大变革。”
另一方面,布线选择也更多。“额外的自由度让问题更易解决,因为布线资源更充裕,”Schultz指出,“例如,通过线间双倍间距可减少交叉耦合,改善电磁特性。若两条信号线并行,可通过类似马蹄形的路径从金属3层绕至金属5层再返回。这些新方案都是可能的。”
其他人对此表示认同。“设计层面的优势相当明显,”Fischer表示,“布线工具更易使用,因为它们无需避开电源网格。此外,由于所有金属层均可直接印刷,我们无需处理复杂的间距分割规则。”
更直接的供电还能提升电源利用率。“更好的电源利用率有助于活性晶体管密度的扩展,”英特尔的Fischer解释道,“电源利用率取决于能否为每个单元提供充足电力,从而提高晶圆上晶体管的实际利用率。采用背面供电后,利用率较传统方案提升了约10%。”
背面供电方案使正面金属间距得以一次性放宽,这或能推迟一至两个节点再引入低电阻金属(如钌)替代铜互连的需求,尤其是在精细间距层。
制造通孔和硅晶片减与所有颠覆性半导体技术一样,背面供电需攻克重大挑战以验证新工艺、提升良率并实现大规模量产,包括:
硅通孔 (TSV) 的蚀刻和填充;将器件晶圆键合到载体晶圆上,然后进行极端的晶圆减薄;精确 的通孔显露(via reveal),以及背面互连与TSV对准,并完成背面金属堆叠和再分布层(RDLs)。
图1:首先制造晶体管与电源通孔(a),接着进行正面多层金属化和介质密封(b)、与硅载体键合(c),最后完成背面供电处理。来源:英特尔
随着背面供电方案的升级,这些工艺难度逐步增加。目前存在三种方案:
第一种是“带电源轨的背面供电网络(BPDN)”,通过背面电源轨的垂直通孔绕行CMOS场效应晶体管(FET)并连接顶部触点。该方案由imec于2019年首创,对前端器件工艺的干扰最小。
第二种方案通常称为“电源通孔”,通过正面通孔连接正面触点,虽复杂度略高但微缩优势更显著。英特尔的PowerVia工艺流程(见图1)已研发近十年。
第三种方案“直连”实现难度最大,但性能与微缩效益最佳。该方案通过背面通孔直接从下方接触晶体管的源极或漏极,需将硅衬底减薄至几乎消失(仅剩10纳米)。
imec近年来持续探索直连方案。“我们的背面供电方案已从CFET(互补场效应晶体管)和纳米片结构演进至直接触点,”Beyne表示,“目标是直接从背面接触源/漏极,这意味着必须严格管控所有工艺公差。早期方案中,光刻畸变后套刻精度达20纳米即可满足TSV需求;但若需接触栅极,则需约3纳米套刻精度。”
光刻工具通过在每个掩模场域修正畸变以实现背面连接与TSV对准。“在此过程中,晶圆需经历键合、衬底去除等‘严酷’步骤,”Beyne解释道,“原以为晶体管位置固定,但工艺畸变会改变其实际位置。因此需通过测量已知位移量,动态调整光刻对准方向。令人惊叹的是,这种方法确实可行。”
其他挑战晶圆背面金属层的存在增加了芯片调试难度(传统调试常通过硅背面进行)。“我们确实失去了部分能力,例如直接切断晶体管连接,”Fischer坦言,“但工程师的智慧在于利用背面高度冗余的特性——调试时可切除部分结构,同时确保供电充足。最终将调试时间缩短至一天半。”
此外,背面集成方案可能改变器件内部的应力分布,进而影响晶体管电学特性。例如,背面金属化与TSV引入的机械应力会改变全环绕栅晶体管沟道的应变状态,直接影响载流子迁移率与驱动电流。
“模拟这些三维应力分布至关重要,”Lam Research Semiverse Solutions高级半导体工艺与集成工程师Sam Sarkar指出,“应力管理对器件性能(尤其是GAA等先进架构)尤为关键。”他强调了晶圆减薄与TSV形成对应力分布和光刻对准的影响:“这些工艺在晶圆处理、对准精度与热预算管理方面带来新挑战。”
保持键合前后晶圆平整度同样困难。“两片平整晶圆键合后会产生畸变,”imec的Beyne表示,“键合设备通过在键合时预弯晶圆来抵消畸变,使最终结果保持平整。但减薄后的晶圆翘曲度是初始两片晶圆翘曲的总和,因此必须从近乎完美的平整晶圆开始处理——初始平整度越高,最终结果越好。”
更棘手的是,背面供电改变了芯片热传导路径。传统正面金属化芯片的热量主要通过硅衬底导向散热器,而背面供电网络(PDN)在器件与散热路径间增加了后端金属层。“这些低导热层导致热阻增加,”Beyne解释,“若能将背面金属层设计为高效导热层,则可抵消劣势。关键在于解决局部热点问题,将热量扩散至更大区域。”
结论背面供电技术有望在2纳米以下逻辑器件中实现,尤其适用于高功耗、高性能场景——其可显著提升开关速度、降低电压降噪并优化能效。
突破工艺挑战需攻克极端减薄、晶圆键合、正背面互连对准及先进器件调试。首代背面供电网络落地后,芯片制造商将直面晶体管源/漏极直连的艰巨任务——这为亚纳米制程开启新一轮技术攻坚。
*声明:本文系原作者创作。文章内容系其个人观点,我方转载仅为分享与讨论,不代表我方赞成或认同,如有异议,请联系后台。
想要获取半导体产业的前沿洞见、技术速递、趋势解析,关注我们!